Vacuum casting is mainly used for small-scale prototype production,
with the advantages of fast time, low cost, and very good market
competitiveness. The materials used to make vacuum casting prototypes
include ABS, PP,PC, What are the production processes of vacuum casting
prototype, such as acrylic, soft rubber, and silicone rubber:
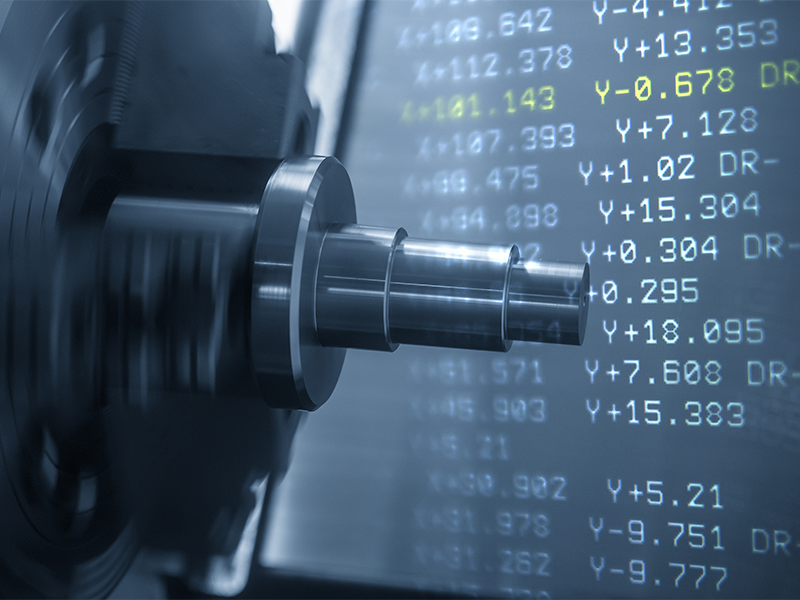
1. Prototype production
Before making silicone molds, it is necessary to make an original
version, which can be produced through CNC machining or 3D printing.
Prototype production is particularly important as it affects the
accuracy and appearance of the product in the later stage.
2. Silicone mold production
Start making silicone molds, mix the silicone and curing agent evenly
The appearance of mold silicone is a flowing liquid, with component A
being silicone and component B being a curing agent. After mixing the
silicone and curing agent evenly, a vacuum exhaust bubble process is
carried out to reduce the generation of bubbles and ensure the density
and appearance of the casting.
3. Silicone curing and product demolding
Pour the silicone that has been evacuated and purged of bubbles onto
the product by brushing or pouring (note: the product or model to be
replicated before pouring the silicone must be coated with release agent
or isolation agent), then brush the silicone onto the product, place
the mold in a specific oven for curing, and after curing is complete,
remove the casting to complete the product demolding.
4. Post processing of castings
The products produced by vacuum casting are usually subjected to
trimming, polishing, and smoothing. Depending on the needs of some
customers, they may also require painting, polishing, spray coating, and
screen printing to ensure that the appearance meets customer standards.
About Jingtianxia Vacuum Casting Manufacturing Case
Jingtianxia has produced a batch of robot shell components for a
professional robot research and development company. In the demand for
small and medium-sized batches, vacuum casting is undoubtedly the best
choice.
Our steps for manufacturing robot shells
-Confirm the drawing design
Our technical team will analyze the drawing structure using DFM,
confirm the CAD design with you, and create the original template
through CNC/3D printing.
-Silicone mold manufacturing
Using product prototypes (rapid prototyping parts, CNC prototypes) to
create silicone molds in a vacuum state, and casting them using
materials such as PU, ABS, etc. in a vacuum state, in order to clone
replicas that are identical to the product prototype.
- Casting parts
Pour the silicone solution into the mold, cure it at a constant temperature, and then cast the product.
-Inspection and delivery
After all the accessories are cast, we will assemble the complete
product and proceed with the next step of surface treatment. The entire
production cycle can be completed within 3 days.
Advantages and disadvantages of vacuum casting:
There are many advantages to vacuum casting processing, as follows:
(1) Suitable for small batch product processing and production, once
an original version is made, it can be replicated based on the original
version, while CNC machining requires a lathe to make prototypes one by
one.
(2) Low cost and relatively short product production cycle. Less
waste and much lower processing costs compared to CNC machining and 3D
printing.
(3) The probability of processing failure is low. As long as there
are no issues with the original version, the replica will naturally not
make any mistakes.
(4) Good mold making operability. After solidification, the soft
molds are transparent or semi transparent, with good tensile strength
and easy cutting and parting.
(5) Good repeatability. The silicone used for molding has good
flowability before curing, and with vacuum defoaming, it can accurately
maintain the detailed structure and decoration of the model.
However, the vacuum replica prototype also has disadvantages, such as
being prone to shrinkage and deformation, as it will shrink after being
heated at high temperatures and cooled, resulting in deformation, with a
general error of about 0.2mm. In addition, vacuum casting prototypes
can generally only withstand high temperatures of around 60 degrees
Celsius, and their strength and hardness are also lower than CNC
prototypes.
Summary
The vacuum casting process has advantages such as small batch size,
low cost, repeatability, and good operability, and is widely used in the
manufacturing industry. At Jingtianxia, we have over 10 years of casting
experience and have established friendly cooperative relationships with
numerous enterprises. We can provide you with the best service
experience and high-quality products. You can upload your CAD drawings
and let us serve your project.