On the stage of manufacturing, processing technology is like dancers of different genres, each showcasing their unique charm. CNC precision machining and traditional machining are two performers with distinct styles. Although they belong to the same field of machining, they have distinct differences in precision, efficiency, and applicable scenarios. Many manufacturing companies are often confused when choosing a processing method: what is the difference between the two? Where are their respective advantages reflected? Next, we will take you through the core differences between these two processing technologies from a personification perspective, providing you with reference for your production decisions.
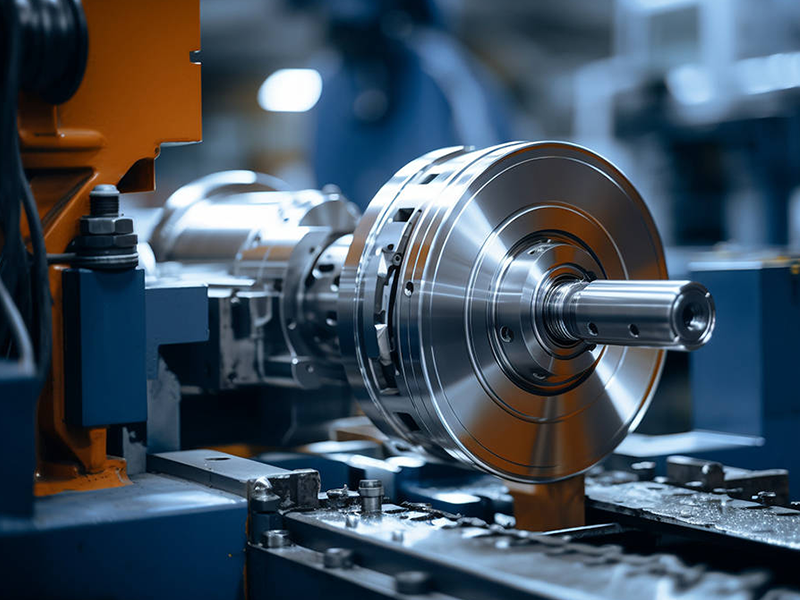
CNC precision machining and traditional machining are like "precision artists" and "practical craftsmen" in the manufacturing industry. Although they are both techniques for creating components, they exhibit different characteristics in multiple dimensions. This article will compare and analyze the core differences between machining accuracy, automation level, applicable scenarios, flexibility and efficiency, cost-effectiveness, etc., to help readers clearly understand their respective advantages and scope of application, so as to make more suitable choices in actual production.
Processing accuracy: a leap from "millimeter level" to "micrometer level"
Traditional machining is like an experienced 'craftsman', relying on the skilled skills and manual adjustments of operators to control machining accuracy. Its machining accuracy is usually in the millimeter level, suitable for machining parts with relatively low precision requirements, such as some parts with simple structures and a large tolerance range. During the machining process, operators need to constantly monitor the operating status of the machine tool, adjust the position of the tool and cutting parameters based on experience, just like a painter controls the strength and angle of the brush with their hand feel.
CNC precision machining, on the other hand, is like a "precise digital artist" who uses computer numerical control systems (CNC systems) to achieve precise control over the machining process. It can achieve micrometer level machining accuracy, which means high-precision components with minimal dimensional errors and extremely low surface roughness can be machined. A CNC system is like an intelligent brain that converts design drawings into precise digital instructions, controlling every action of the machine tool. Whether it is linear or circular motion, it can strictly follow the preset trajectory, as if carving on the material with a precise ruler, ensuring that every detail meets the design requirements.
Automation level: transition from "human led" to "intelligent control"
The production process of traditional machining largely relies on the skills and experience of operators. From installing workpieces, adjusting tools to setting machining parameters, all require manual operation by operators. Just like a chef who controls the heat and seasonings in the kitchen with years of experience, every step cannot be separated from human participation. This processing method has high requirements for operators, relatively high labor costs, and production efficiency is easily affected by the status and skill level of operators.
CNC precision machining achieves a high degree of automation. Once the machining program is input into the CNC system, the machine tool can automatically complete the entire machining process according to the program, including workpiece positioning, tool replacement, and adjustment of machining parameters. Operators only need to program and clamp the workpiece before processing, and perform necessary monitoring during the processing. This is like an intelligent robot working tirelessly according to pre-set instructions, greatly reducing human input and improving production efficiency and processing consistency. The CNC system also has real-time monitoring and fault diagnosis functions, which can timely detect problems during the machining process and take corresponding measures to ensure the stability and reliability of the machining process.
Applicable scenarios: subdivision from "mass production" to "precision customization"
Traditional machining, with its relatively simple operation and low equipment cost, is more suitable for mass production of parts with simple structures and low precision requirements. For example, in the processing of some ordinary mechanical parts, such as standard parts, simple flanges, gearboxes, etc., traditional machining can leverage its efficient and stable advantages to quickly meet the needs of mass production. Just like workers on an assembly line, who focus on repetitive and simple operations, they can produce a large number of products in a short period of time.
CNC precision machining has demonstrated unique advantages in the field of precision component processing. It is suitable for processing various complex shaped parts, such as high-precision bearings, complex structural components in the aerospace industry, precision connectors in the electronics industry, etc. These components often have requirements for high precision, high complexity, and high surface quality, which traditional machining cannot meet. CNC precision machining can achieve the processing of complex surfaces through programming, just like an artist creating complex sculptures that can accurately present every detail of the design. At the same time, for small batch or even single piece precision component processing, CNC precision machining can efficiently complete tasks with its flexible programming and fast adjustment capabilities.
Flexibility and Efficiency: Finding a Balance between Change and Stability
Traditional machining requires operators to readjust machine parameters, replace tools, or even reinstall workpieces when faced with product design changes or processing requirements adjustments. This process often takes a long time and has relatively poor flexibility. Just like a traditional craftsman, when the customer's needs change, they need to rethink and adjust the production process, which consumes a lot of time and energy. However, in stable mass production, traditional machining can maintain high production efficiency because operators are already very familiar with the machining process and the state of the machine tool is relatively stable.
CNC precision machining has strong flexibility. When different parts need to be processed, simply change the processing program without the need for large-scale adjustments to the machine tool. This is like a multifunctional smart device, which can achieve different functions by replacing different software programs. When facing the production needs of multiple varieties and small batches, CNC precision machining can quickly switch processing tasks, improving the flexibility and adaptability of production. At the same time, CNC precision machining has a high degree of automation and stable processing, which can achieve high production efficiency while ensuring accuracy. Especially when processing complex parts, its efficiency advantage is more obvious.
CNC precision machining and traditional machining are like two protagonists on the manufacturing stage, each shining with unique brilliance. CNC precision machining has become a "leader" in the field of precision manufacturing with its micrometer level accuracy, high degree of automation, and powerful ability to process complex parts; Traditional machining stands firm in its position due to its easy operation, low equipment cost, and stability in mass production. The differences between the two in terms of processing accuracy, automation level, applicable scenarios, flexibility, and efficiency are precisely to meet the diverse production needs of the manufacturing industry.